
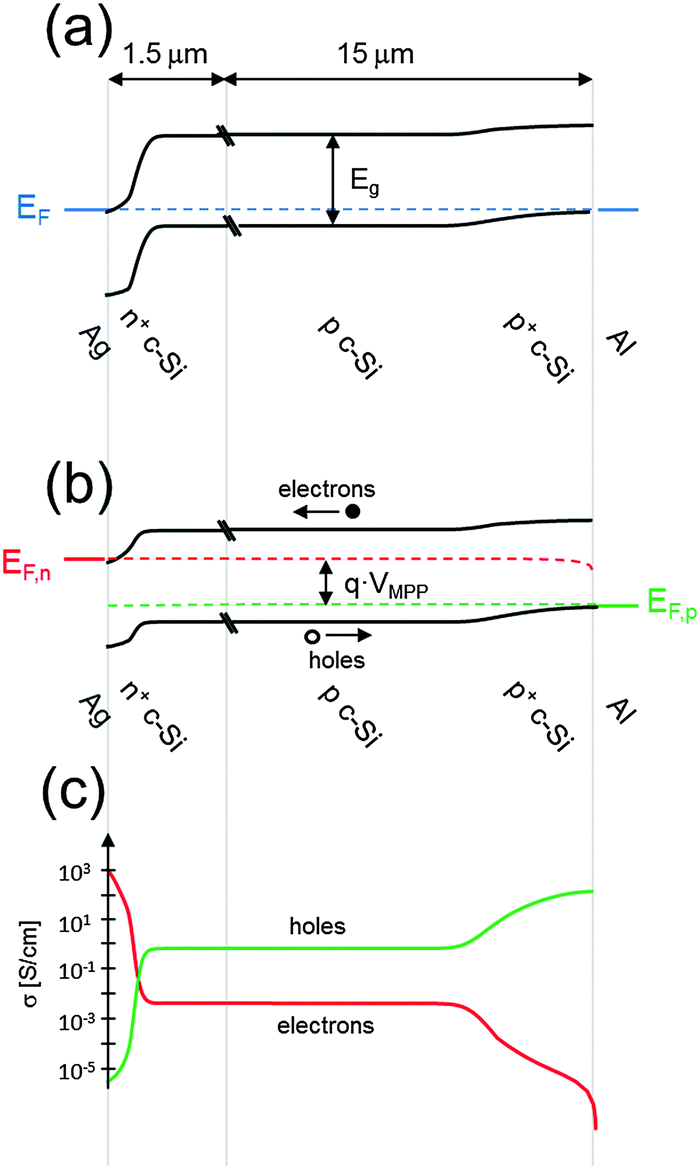
Compared to the thermal diffusion method, ion implantation also allows an excellent control over the doping profile. It does not require the etching of the phosphosilicate glass formed during the diffusion process or the additional edge isolation step. Of these methods, ion implantation, when applied to the solar cell fabrication, has many advantages compared to the conventional thermal diffusion method. There are many ways in creating the emitter, including the standard diffusion process, ion implantation, and epitaxial growth. The emitter is usually formed by diffusing the dopant atom into a silicon wafer surface. The formation of the emitter in fabricating solar cells is one of the critical processes in the solar cell fabrication process. PC1D simulation based on these results shows that, for p-type implanted solar cells, increasing the annealing temperature and time abruptly decreases the efficiency ( %), while, for n-type implanted solar cells, deep junction annealing increases the efficiency and, especially ( %) for backside emitter solar cells. This is due to the abrupt decrease in the bulk lifetime of the p-type wafer itself from 178 μs to 14 μs. However, for phosphorus emitters the implied decreases from 622 mV to 560 mV and the increases with deep junction annealing. QSSPC measurements show that the implied of boron emitters increases about 15 mV and the decreases by deep junction annealing even after the activation due to the reduced recombination in the emitter. Boron emitters were activated at or higher, while phosphorus emitters were activated at. P-type and n-type wafers were implanted with phosphorus and boron, respectively, for emitter formation and were annealed subsequently at 950 ~1050 for 30 ~90 min for activation.
